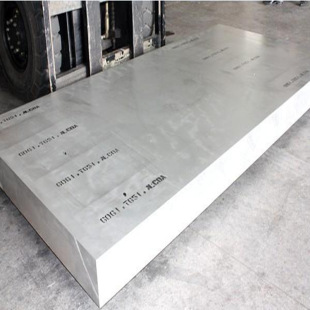
連續擠壓整個過程都在密閉的真空狀態下進行,帶坯經過擠壓從模具口出來后及時冷卻和密封非常關鍵,經過我不斷改進,優化設計冷卻液噴淋裝置和密封系統。該系統使生產帶坯時能使用普通H13材料做擠壓模具而不會變形(用高溫合金做模具太過昂貴,400元/公斤)大幅降低模具成本,同時擠出帶坯沒有表面氧化和氣泡現象,帶坯變形量小(小于0.1mm尺寸均勻,所以無需銑面,產品的成材率可達到75%左右。連續擠壓技術生產的花紋鋁板采用上引無氧銅桿為原料,上引無氧銅桿的純度及氧含量更容易控制,可以達到高純高導花紋鋁板的要求(Cu+A g≥99.99%氧含量≤5ppm導電率≥101%IA CS花紋鋁板分析測試結果 交貨期短,連續擠壓技術生產花紋鋁板使整個工藝流程縮短(模具和銅桿準備好的話,2個小時預熱腔體模具即可開機,2~3噸/小時帶坯產量)不但降低了整個銅板帶生產線的運營成本,而且對企業節能減排、綠色制造目標的實現貢獻巨大。應用 連續擠壓技術生產花紋鋁板不僅具有半連鑄-熱軋法優異的力學性能,還具有高純、高導、低氧含量(Cu+A g≥99.99%氧含量≤5ppm導電率≥101%IA CS等優點,可廣泛應用于電力、電器、電子、通訊行業中制作高端產品組件,如光伏銅帶、同軸射頻電纜、變壓器銅帶、電子沖壓件、貴金屬復合帶、計算機微型散熱器、柔性印刷電路板等領域。結論 連續擠壓技術生產花紋鋁板不僅具有組織致密、晶粒細小等良好的力學性能,還具有高純、高導、低氧含量(Cu+A g≥99.99%氧含量≤5ppm導電率≥101%IA CS等優點,該技術還具有生產流程短、生產效率高、產品成材率高、交貨期短等特點。
region-detail-gallery